Copy link
Lean Six Sigma
Last updated: 05/15/2024
Key Points
- Common quality improvement planning tools include Model for Improvement, Lean Six Sigma, Plan Do Study Act (PDSA), Key Driver Diagrams (KDD), and Run charts.
- Lean methodology focuses on the voice of the customer to understand what is important to them and to identify and eliminate or reduce waste for non-value-added activities.
- Understanding steps that are considered “value-added, business-value-added, and non-value-added” is helpful in removing waste in a process or system.
- Lean Six Sigma combines improvement in flow and value with reduced error and variation.
Introduction
- The Six Sigma methodology originated in Motorola Corporation in the 1980s with the goal of reducing variation and errors. Two fundamental goals of Six Sigma are a virtually error-free process and a large focus on reducing variation. In a Six Sigma process, the frequency of an error falls six deviations from the mean (about 3.4 errors per million).
- Lean methodology has its roots in Japanese manufacturing, particularly Toyota. Lean methodology focuses on the voice of the customer to understand what is important to them and to identify and eliminate or reduce waste for non-value-added activities.
- Lean focuses on using data/numbers to objectively evaluate and identify opportunities for improvement (i.e., without baseline data, how do we know that we have a problem? Is this an actual problem, or does an individual have a single concern?).
- Lean strives to improve the flow of everyday work (i.e., is there a way to improve the organization of the pharmacy kit available to the anesthesiology team, or how can we improve the location of patient charts to avoid having team members walk around the preoperative holding area to locate the chart?).
- Lean Six Sigma is a synergized concept of Lean methodology and Six Sigma that combines improvements in flow and value with reduced error and variation.
Lean Six Sigma
- The 7 steps of Lean Six Sigma include:1
- Problem statement (define the project and the scope of the project)
- Understanding process/situation before
- Identifying quick wins/immediate counter measures
- Causes and improvements
- Implementation plan
- Process and situation after
- Standardization and sustaining a new process.
- Lean Six Sigma methodology asks: “How do we reduce ‘waste’ in a system to make it more ‘lean’?”
- Lean improvement strives to eliminate waste by utilizing a “systematic approach to identifying and eliminating waste (non-value-added activities) through continuous improvement by flowing the product at the pull of the customer’s pursuit of perfection.”2
- Lean methodology aims to enhance effectiveness by mitigating defects and seeking errors less than 1/106 (to the sixth power) in frequency.
- The Lean approach is based on five major principles (Figure 1):
- Defining value (what a customer is willing to pay for) based on the “customer’s perspective.”
- Identifying value streams required to provide to the customer
- Making the value-added steps move smoothly
- The customers “pull” services as needed (as opposed to a “push” system).
- Everyone is pursuing “perfection.”2
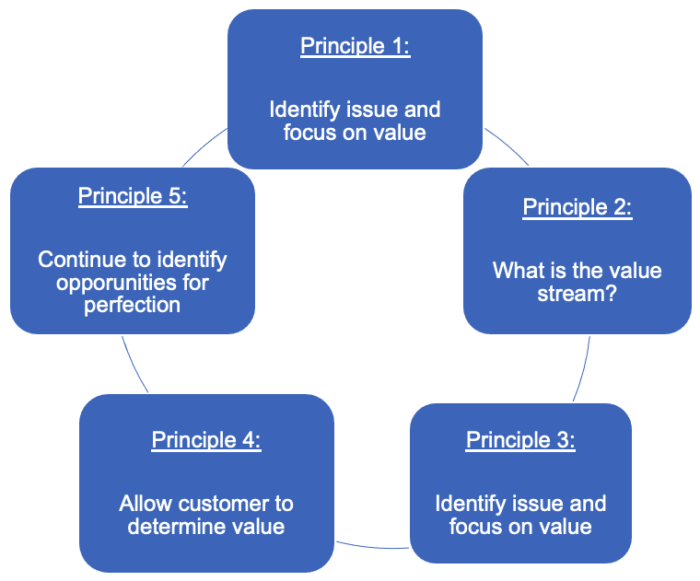
Figure 1. Five principles of lean thinking. Adapted from Womack JP and Jones D. Lean Thinking. Simon & Schuster, 2003.3
Value Stream Mapping
- Lean utilizes value stream mapping as a tool for identifying wastes in a current state and designing solutions for this waste.
- This tool can examine a process and help the teams to better understand the flow of a system as a customer moves through it.
- A similar tool that is used in the Model for Improvement would be Failure Mode Effects Analysis (FMEA).
- These steps can further be identified as steps that add value or decrease waste.
- Value is defined as added entities that seek to change the “deliverables” of a process, such that the customer is aware of the change and willing to pay for the task to be done correctly the first time.
- Waste could be defined as unnecessary or superfluous energy or items. (i.e., unused supplies, unnecessary time spent waiting, extra steps taken when a more streamlined process could be put into place)
- Goals include eliminating non-value-added tasks when possible and minimizing business-value-added tasks through Lean methodology. Below are the definitions of these tasks:
- Value-added: The client is aware and is willing to pay for it (e.g., prefilled syringes with diluted pressors).
- Business-value-added: These do not add value but are required by regulation or law (e.g., medications put through quality control testing in pharmacy).
- Non-value-added: These do not impact the customer or the business (e.g., locating medications or walking to the pharmacy to obtain medications when not stocked appropriately).
- Once a process is understood, another tool that Lean uses is a Fishbone diagram (Ishikawa diagram) to assist with further examining etiologies of the central issue (Figure 2). Which items contribute to the ongoing process that has been identified as an area of improvement?
- Possible etiologies may include environmental factors, methods, machine, measurement, man, and materials.
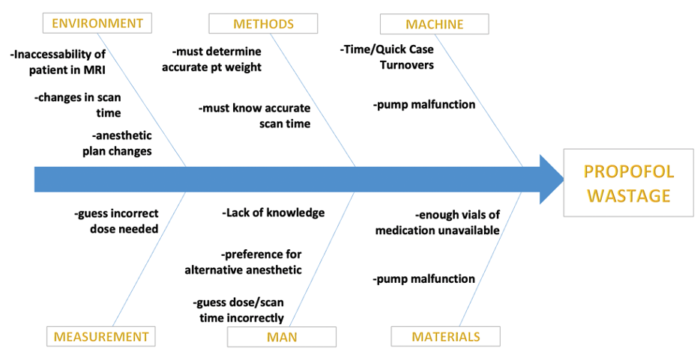
Figure 2. A fishbone diagram/Ishikawa diagram is an example of how to examine etiologies of the problem being addressed. Courtesy of Megha Kanjia.
5S
- In Lean methodology, there are often “quick wins” or opportunities to improve the immediate workspace, streamline the process, and remove excess waste. This could mean that unnecessary supplies are removed from a work area or necessary items are restocked appropriately. Wasted time can be spent searching for necessary items as well as sifting through things that are not necessary given the disorganization of a work area. By following the “5 S” idea, one can relatively quickly streamline a process based on the organization of a particular area. By utilizing “5 S” to focus on a “quick win,” one may be able to move a process forward without a longer-term project that may be more challenging to implement based on significant process changes and buy-in that could be required from various team members.
- The purpose of 5S is based on five Japanese principles for workplace organization to promote standardization and decreased process variability (Seiri, Seiton, Seiso, Seiketsu, Shituke)1
- Sort
- Straighten
- Scrub/Shine
- Standardize
- Sustain
References
- Lean belt certification training manual. Texas Children’s Hospital Business Process Transformation. October 2017.
- Langley GJ, Nolan KM, Nolan TW, et al. The improvement guide: A practical approach to enhancing organizational performance. Jossey-Bass & Wiley, 2014. Pg 1-5, 463-465.
- Womack J, Jones D. Lean thinking: Banish waste and create wealth in your corporation. New York, NY; Free Press, Simon and Schuster, Inc., 2003. Link
Other References
Copyright Information
This work is licensed under a Creative Commons Attribution-NonCommercial-NoDerivatives 4.0 International License.