Copy link
Failure Mode Effects Analysis
Last updated: 05/24/2024
Key Points
- Quality improvement (QI) is a science of methodical planning, multiple iterations, and interventions to yield improvements in a process or area. QI projects should follow a valid scientific method and attempt to monitor improvement over time and reflect sustainability.
- A common QI planning tool is failure mode effects analysis (FMEA).
- Process mapping tools include flow diagrams, value stream mapping, and supplier-inputs-process-outputs-customers (SIPOC) diagrams.
- FMEA can be used as a standardized tool to understand opportunities for failure once a process is documented through analysis of failure modes, causes, and consequences of a failure.1
Background and Model for Improvement
- QI is a science of methodical planning and multiple iterations and interventions that yield improvements in a process or area. It combines ideas of associating effective processes with clinical practice into practical methods to improve overall patient care and processes. Aligning the organization’s goals and leadership priorities is also crucial for project planning and execution.
- The Model for Improvement utilizes a foundation based on three crucial questions:
- What are we trying to accomplish?
- How will we know that a change is an improvement?
- What changes can we make that will result in improvement?1
- The initialization of a QI project should start with obtaining baseline data and examining the current process. This can be done by identifying 5-7 steps that outline the major steps from start to finish; this would be the initial process map (Figure 1).
- By utilizing a process map, further opportunities for failure and interventions can be identified by following an FMEA process (Figure 2).
- Analysis of opportunities for failure can expose any areas of opportunity and ensure that appropriate stakeholders are involved and all the relevant team members are engaged from various areas.
- Allowing the weaknesses in the process to be analyzed will help form a more streamlined final process.
- The process may undergo multiple iterations before a final process is in place.
- Finally, sustainability should be considered as the interventions are placed in a project. Understanding how the new process will continue after the project is completed is crucial.
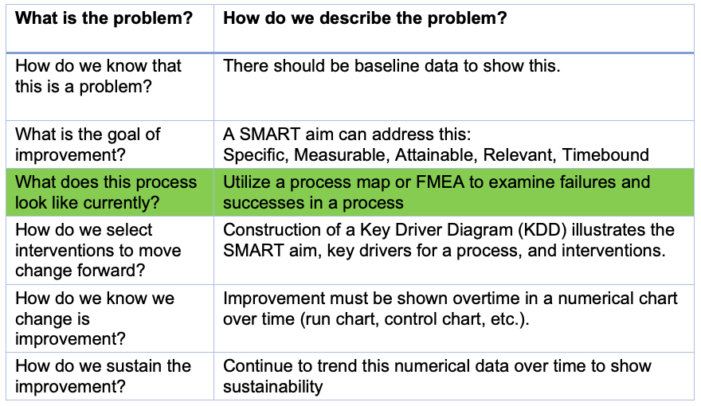
Table 1. Model for improvement questions for project planning (FMEA highlighted in green)
- FMEA asks the following questions (Table 2).
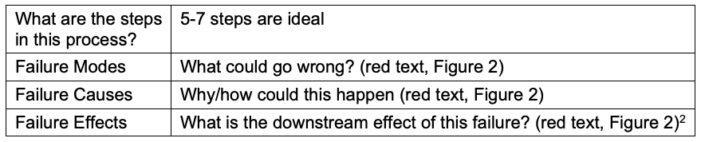
Table 2. FMEA questions
- By asking the FMEA failure questions listed in Table 2, teams gain a better insight into the problem and have an opportunity to mitigate possible failures and problems before they occur.
Examples of a Process Map and FMEA

Figure 1. Example of a process map: A process map can identify a current process, ideally focusing on 5-7 steps to outline major steps. This can be used to start the construction of an FMEA (Figure 2.) Courtesy of Megha Kanjia.
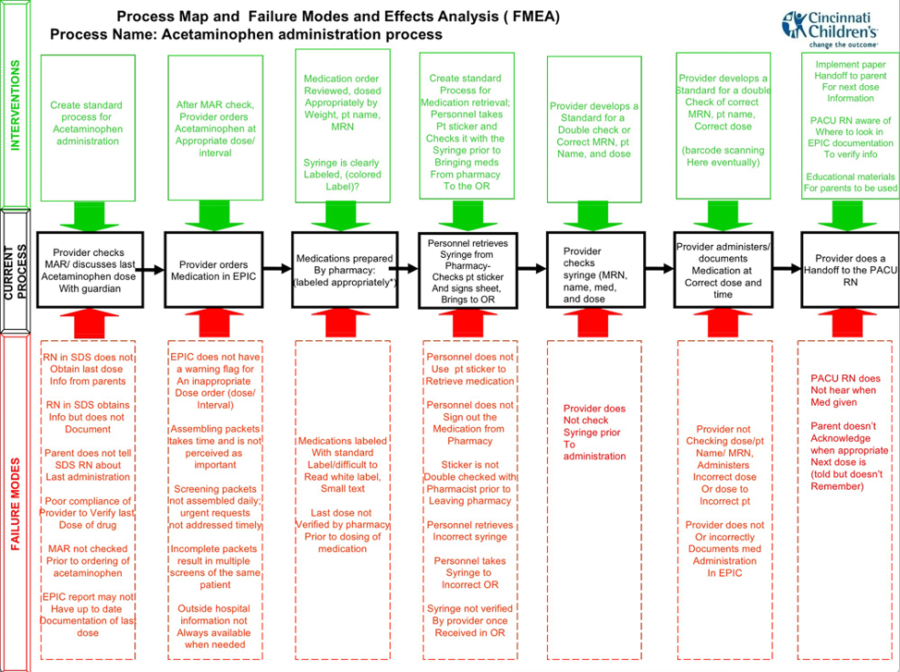
Figure 2. FMEA of a process outlining a current process (black boxes with arrows - administration of acetaminophen in the perioperative area), failure modes (red boxes- outlining opportunities for failure or gaps in process), and interventions (green boxes – how the process looks when it follows the desired process). Courtesy of Megha Kanjia.
References
- Langley GJ. The Improvement Guide: a Practical Approach to Enhancing Organizational Performance. Jossey-Bass, 2014. Pg 1-5, 410,423, 463-465.
- Failure Mode Effects Analysis Tool. Institute for Healthcare Improvement. Link
Other References
Copyright Information
This work is licensed under a Creative Commons Attribution-NonCommercial-NoDerivatives 4.0 International License.